What Makes 800T the Original and Only True 800-Speed Tungsten-Balanced Film for Still Photography
Posted by Brian Wright on

CineStill has made unique color films available for still photographers for over a decade now. Beginning with our small-batch beta films — making motion picture film compatible for standard photo lab processing and printing for the first time ever! Shortly followed up by the first factory finished versions of 800Tungsten & 50Daylight “Xpro C-41” — based on scaling our original “Premoval” process for expanded worldwide availability. And now to our further improved manufacturing of 800T, 400D and 50D — marrying advanced motion picture technology with professional photography components and specifications, in 135, 120 and 4x5 formats. We have always strived for consistency and technical excellence, while championing the unique characteristics and imperfections of film. But there still is a real difference between a predictable novel quality and a true deficiency. In this post-digital age, it is more important than ever for those who choose to shoot on film (whether amateur, professional, or anything in between) to get both their time and money’s worth. Ultimately, we encourage everyone to shoot more film, any film, and find what works best for you! However, it is our responsibility to manage what consumers can expect from CineStill film, and why their experiences may differ should they choose to go elsewhere.
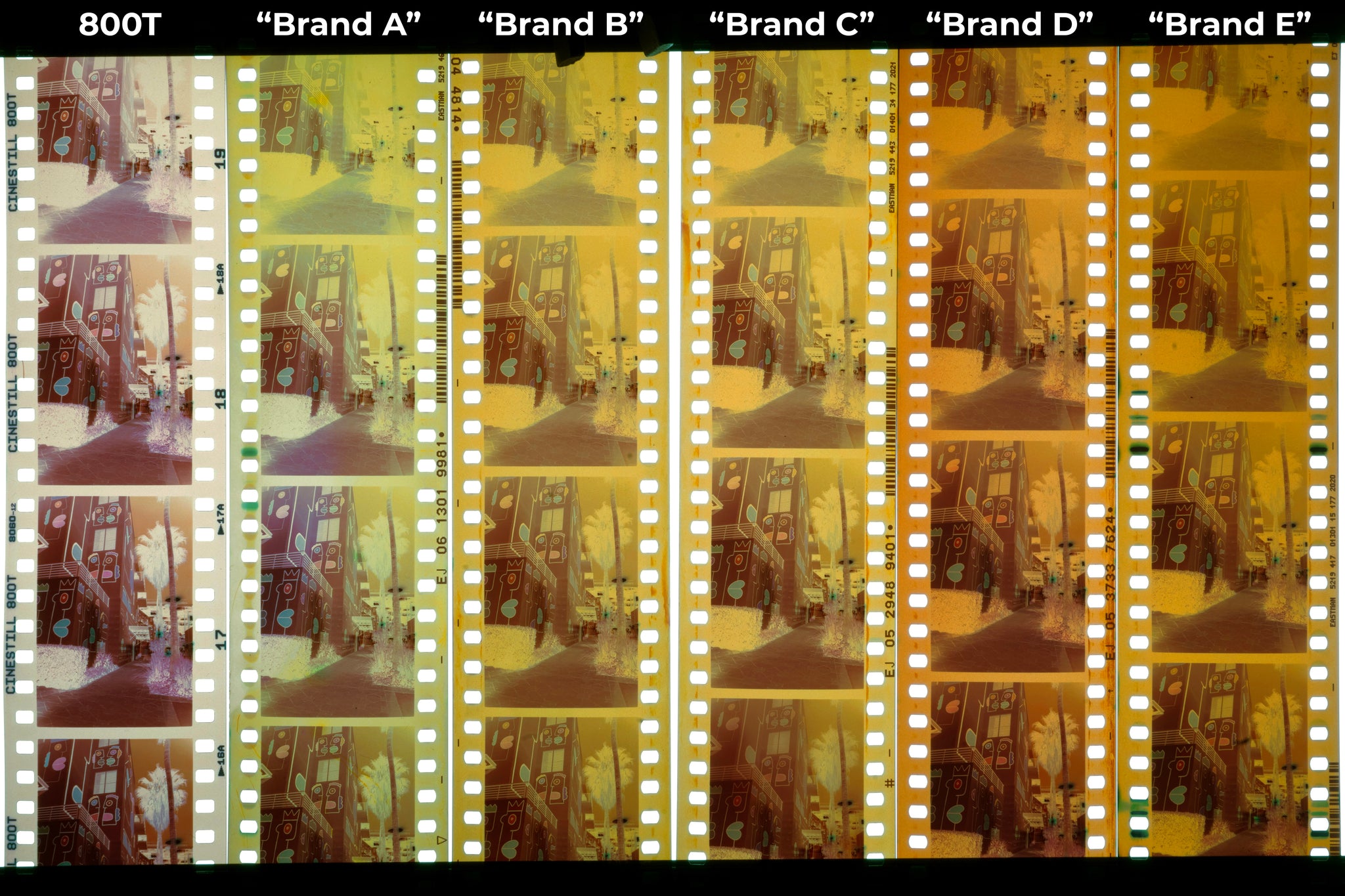
When searching for CineStill films have you come across any “brand new” color films “made by” random brands lately? Are their claims strikingly similar somehow? Have they cracked the CineStill code? No, they have not… Through thorough testing and quality assurance, we have concluded that true 800T — utilizing our meticulous and unique production process — is the only color film that can stand behind the claim of being both 800-speed and Tungsten balanced. This article will further explain how we came to this conclusion and go into detail showing the results of our extensive testing. We are not here to be nit-picky or point fingers and name names — which might get a little confusing — but some names may sound familiar to you by now. Those “800T” imitations and “400D” generics (repurposed from existing 500-speed or 250-speed motion picture film, respectively) are not representative of the original motion picture film’s quality nor the performance of CineStill films’ sensitivity and color fidelity. Although they may replicate the signature CineStill red halation glow, they are only somewhat comparable to expired film, in that they appear age fogged with shifted color-balance and exhibit a slower effective film-speed (200-400 ISO at best) resulting in a film not suitable for proposed use, let alone low-light photography; that is unless you like underexposed/expired film. For those looking for fresh film, we are fortunate to still have several other excellent high-speed color films available today (even with the recent unavailability of 400H and C200) — from UltraMax and Portra 400 to Lomo 800 and Portra 800 — but 800T is still the only tungsten-balanced, true 800-speed film made for still photography. Anything else, isn’t…
Original 800T
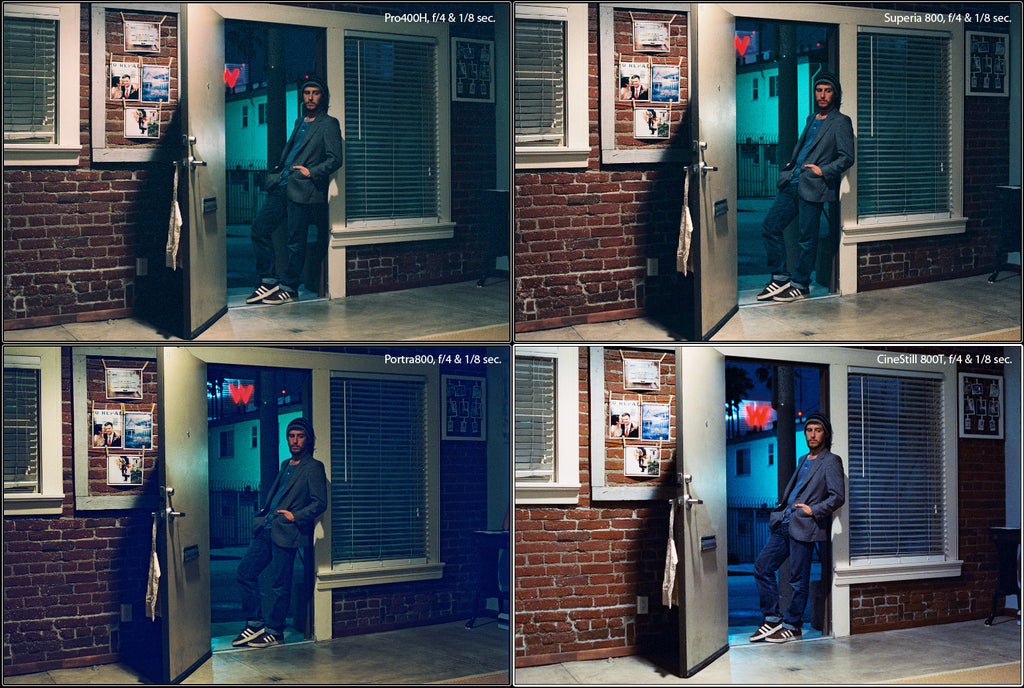
For us, this all started around 2010 with our desire for more quality color films to enable more film photographers to shoot more film in more situations — specifically in low-light. Amidst a deluge of film discontinuations — from the NC and VC varieties of Portra to 800Z and 160C; from Neopan 400 and 1600 to Plus-X and BW400CN; then there was the slide films: Astia 100F, Sensia 400, Provia 400X, Ektachrome 64T, E100G, E100GX, E100VS, E200… and the list goes on and on — it appeared to be the film apocalypse... But long before the 800T or Cine still photography terms were conceived and adopted to identify any products for film photographers, we were actively encouraging and helped many other small businesses in the analog renaissance, and have continued to cheer-on all who have shared this passion for analog advancement. Many others at that time thought we were crazy, but if no one else was going to make motion picture technology accessible for still photography then we were going to at least try. In fact, we have been very open about our research and results from previous prototypes, and have cautioned the various pitfalls (from fogging to ferrotyping) which produce degraded film that does not hold up to the current quality standards that photographers expect. Still, our original Premoval process remains a trade secret and no other business has been able to successfully bring a comparable product to market for over 10 years. Although some have tried and claimed to have done exactly what CineStill does, the truth is: none have. We have always supported more quality films being made available, and anyone is still free to find their own way to emulate the results and quality of CineStill film, using the experience and advice we have openly shared. A product should just do what it claims to do.


The decision to release our first film product at a higher exposure index of 800 under incandescent light was made only after analyzing the Sensitometric Characteristic Curves and results from our first fully successful beta tests. And no, it wasn’t based on reflections off the back of the film or baseplate of the camera, nor clever/disingenuous marketing. Sure, we could have easily made a lower quality film with reduced film-speed and treated it like expired film — which could only be usable when overexposed and manipulated with scanning software — but we didn’t want to just settle for a novel concept and cut corners to market a gimmick that was easier to reproduce yet underperformed. After years of research and development — abandoning many ultimately unacceptable trials — we finally perfected a film that we wanted to shoot ourselves, which also fulfilled a need for photographers just like us. Our film not only outperformed the expectations of “box speed” under warm light and was able to be push processed to even higher ISOs with added development (without just raising base fog), but it was also optimal for straight scanning and darkroom printing.

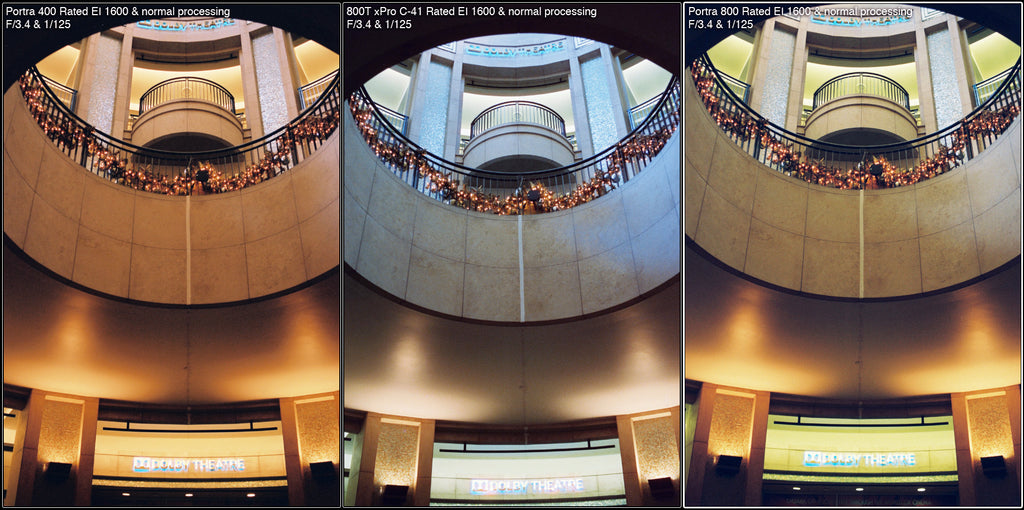
After conclusive comparisons to all other high-speed films available at the time, we confirmed that our film performed at its best when rated at a box speed of EI 800 in tungsten-balanced light — rather than say 500, 640, or 1000. We also found that it could even be push processed up to 3 stops further without any base fog issues. Our belief was (and still remains) that there really is no good reason to release a new film which cannibalizes an already crowded niche market, unless instead it offers unique qualities that will enable more photographers to shoot more film in more situations — while also supporting the continued sustainability and growth of film manufacturing. Our film did just that! Based on thorough testing and confirmed results from many trusted beta testers around the world, we chose to use “800T” as our product identifier — since the mark was available for unique use in the photographic market and had been long abandoned in the motion picture industry back in 2004. Since 2013 our flagship film has been commonly identified as simply “800T” by photographers, resellers, and labs around the world.
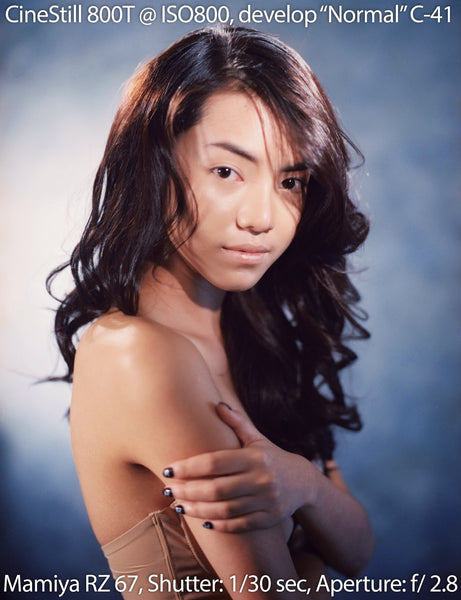
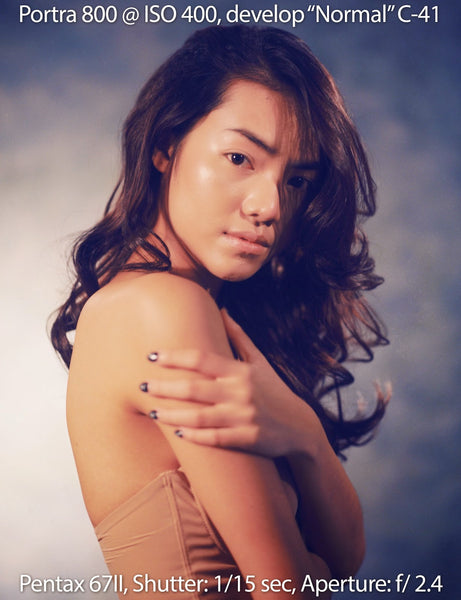
CineStill Imitations
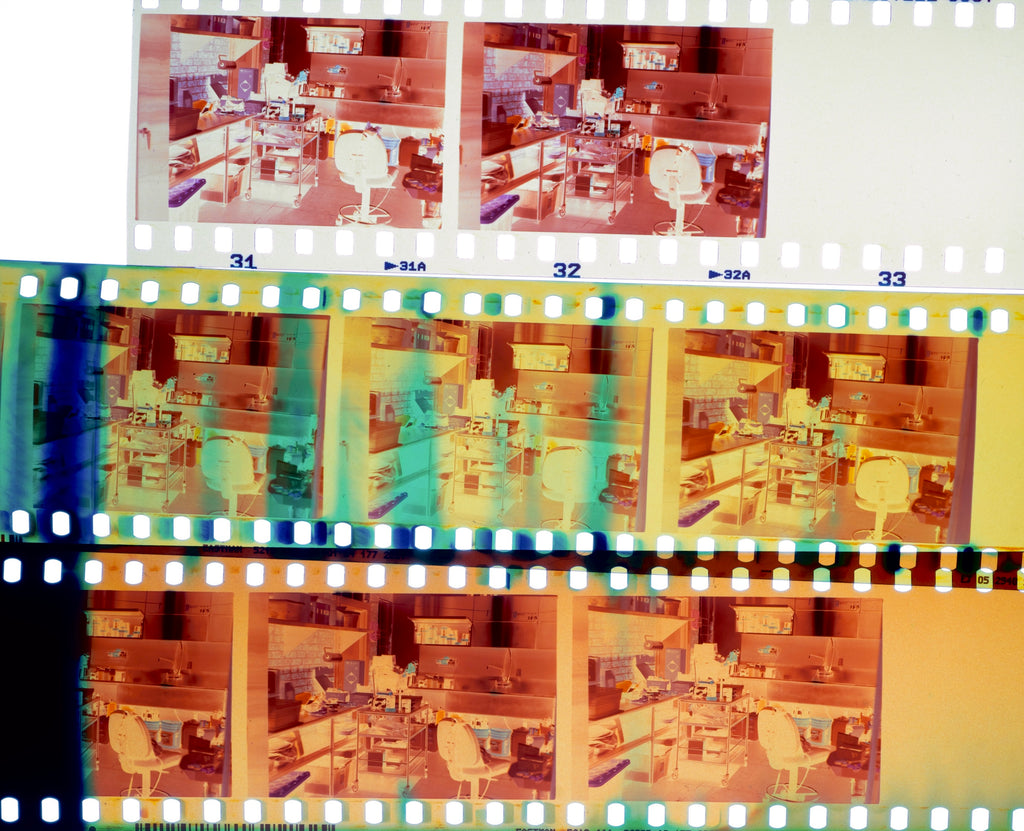
In the years following the successful launch of CineStill’s 800T brand, several other businesses in the western world were inspired to attempt to replicate something similar — by simply soaking leftover motion picture film in a corrosive solution, washing the rem-jet layer off under tap water, then exposing the sensitive emulsion to heat to dry (all of which we warned would ruin the film and cause it to age rapidly). It is said that, “Imitation is the sincerest form of flattery…” Such imitations were welcomed additions to the analog renaissance, and were branded at lower suggested speeds (e.g. Cine200 and 400T ) to help compensate for the inherent base fog and reduced sensitivity caused from “doing what anyone could do” the easy way, but sadly they did not last.
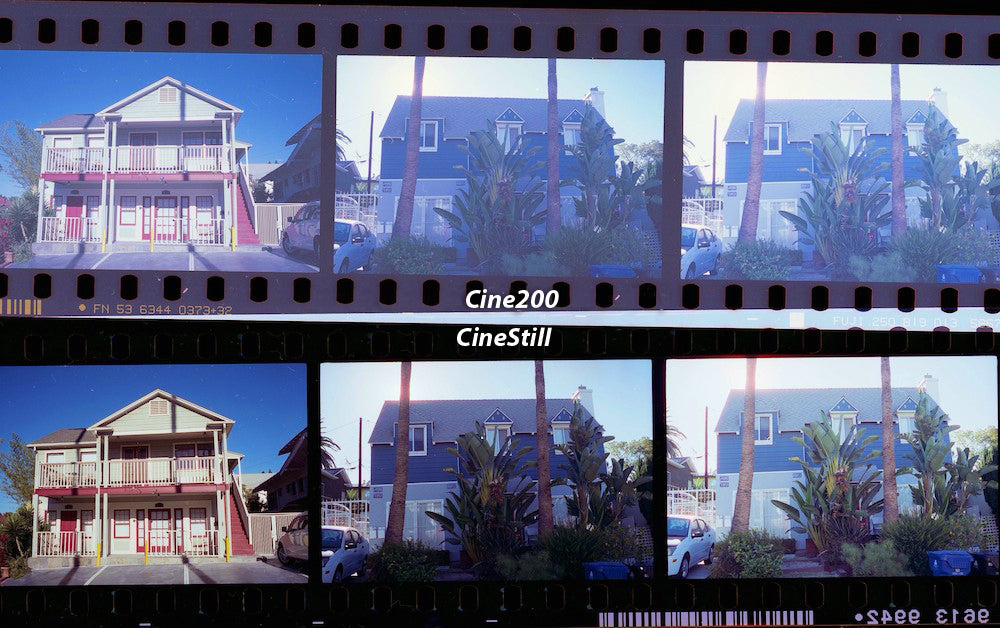
Successfully removing the jet-black layer from motion picture film prior to exposure is very very difficult to do without damaging it — by contaminating the emulsion, fogging the sensitive color layers (which are responsible for the film being tungsten-balanced), or decreasing the effective film speed. And even once the film has been “washed” of its rem-jet layer (along with some of the precious color, filtration, antenna sensitizing dyes, and protective layers) it must be developed immediately or it will begin to expire within weeks. Our previous research proved to us that anything derived from a more conventional removal process immediately yielded fleeting results which quickly faded away and disappointed. We invested in and tested thousands and thousands of feet of film on novel prototypes and trials before we produced a product which we were confident enough in the quality and stability of to offer it to the general public. What we did is not as simple as others may believe, and we have continued to iterate and improve our manufacturing to extend shelf-life and performance with every batch — investing back into R&D for new manufacturing processes, machines, equipment, facilities, and in our small team; to innovate and support quality assurance for the community.
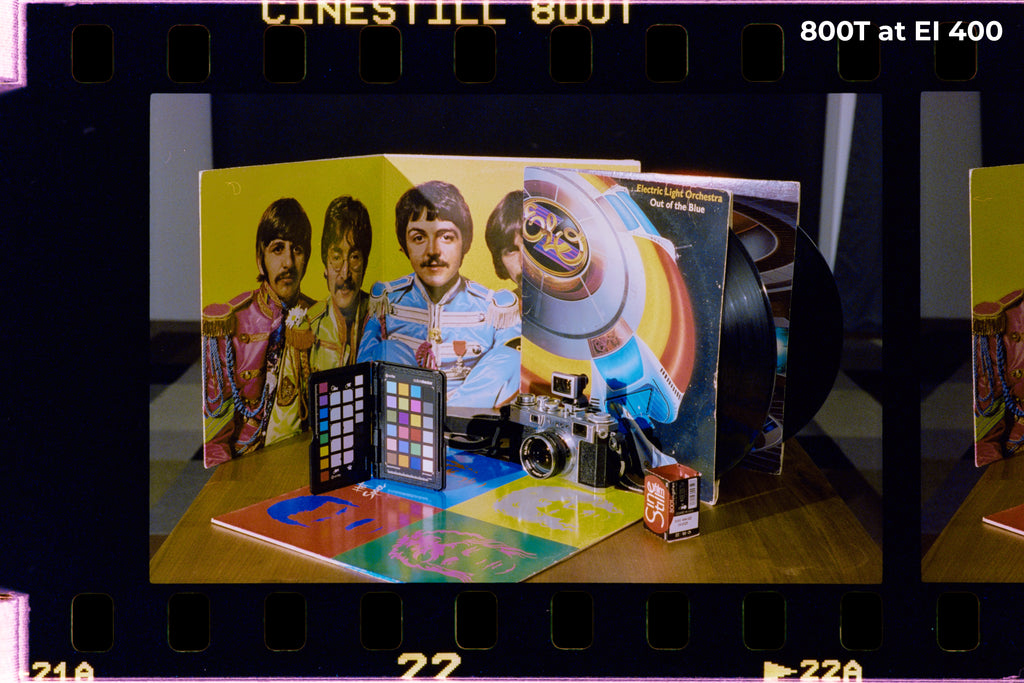
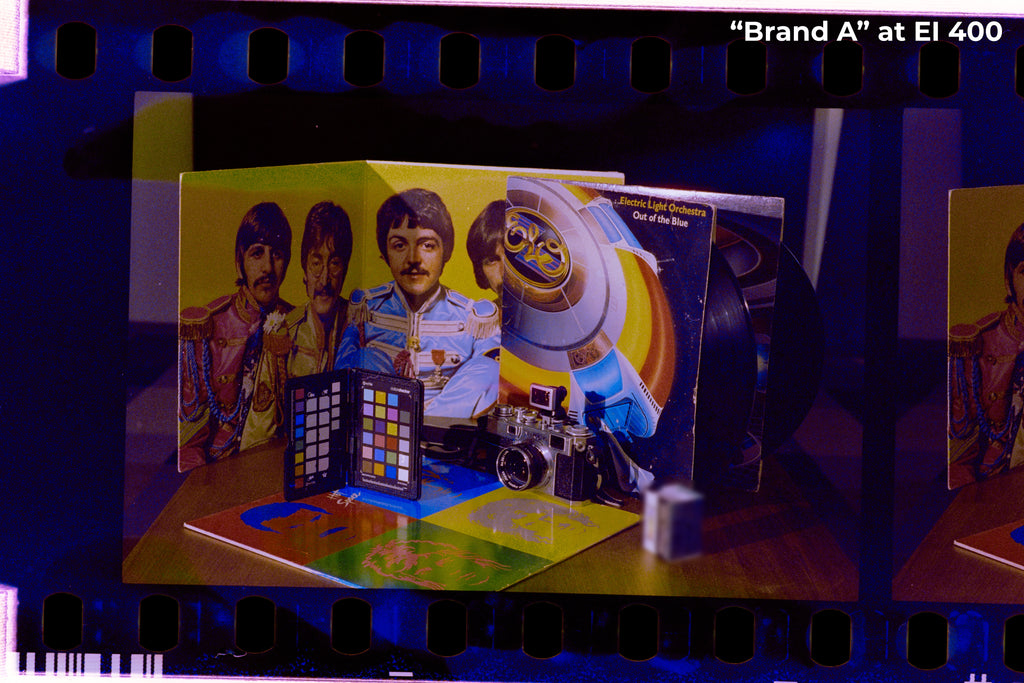
Unfortunately, imitation products released at that time proved to be substantially inferior in quality and performance, and were never improved upon, so each of these products were discontinued by the companies making them. There was also an unfortunate negative effect on our reputation and the perceived quality of our film (and possibly all film) at that time, based on negative experiences with these other films and how they were marketed similarly. For a certain amount of time, some photographers and labs thought that any newly dubbed “Cine” still film products were all just respooled motion picture film or were contaminated and of poor quality, and many labs expressed concern about or downright refused to process any film with motion picture affiliations (our brand included) for fear of disappointing customers or damaging their machines with remaining rem-jet. Our small team overcame those misconceptions a long time ago with diligent community engagement and rigorous quality assurance.
We will always feel a sense of responsibility to ensure that motion picture film maintains a reputation of quality and reliability, and any film packaged for still photography should not be damaging to the analog experience. Fresh CineStill color film not only has higher speed and preserved quality, but also is manufactured for still photography with tried-and-true staked steel cassettes with DX codes (135) or premium paper backing (120), edge-printed frame numbers and stronger KS (Kodak Standard) perforations; without the rem-jet, contamination, motion picture edge signing or BH (Bell and Howell) perforations — which were prone to tearing. While the value of these details is in the eye of the beholder, we maintain high standards — and we are proud to distinguish ourselves with those standards in mind. We now enjoy a supportive analog community who recognizes Cine still films as tools that can be relied upon to create their best work. But sadly history sometimes repeats itself…
Fake 800T
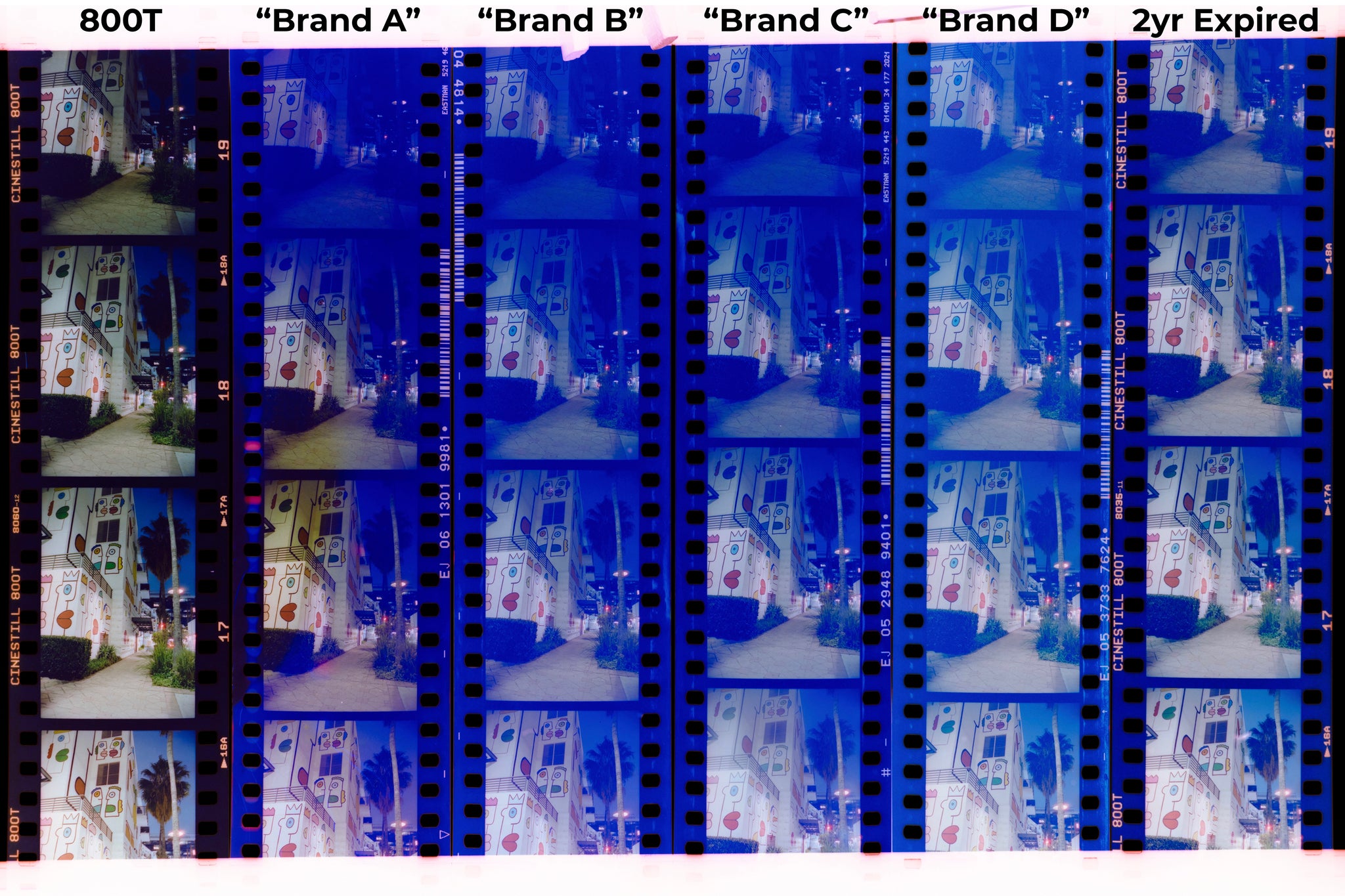
More recently, in 2022 a wave of generic, confusingly similar and even counterfeit imitation products started popping up in China and greater Southeast Asian marketplaces. Even though it has proven to be a struggle for us to supply the demand for our own film there, we then began purchasing samples and testing these films against our QA standards (and continue to do so); hopeful that someone else could meet the standards to supply even more quality film to the whole world of analog photography. More supply means more people shooting film! Disappointingly, some of them turned out to just be recklessly respooled motion picture film, but a few proved to have the rem-jet poorly removed prior to packaging (which at first glance was promising). Our testing continues to identify a range of issues, including varying degrees of contamination, reduced sensitivity, age/heat/chemical fogging, and consistent marks and light leaks — resulting in a degraded film that underperforms even when compared to over 2-years old expired 800T (which wasn’t even cold stored), despite the samples being in-date. While the freshest samples (with the most recent emulsion codes on the motion picture edge print) appeared less expired, as they approach their expiration dates (which many carelessly don’t have) they quickly show further increased base fog and color cast – confirming our own research that any contamination continues to rapidly age the film even after repackaging.








Although most of these films are spooled into varying 135 cassette designs with different materials used, one thing we found in common (besides the appearance of 2-3 years expired film) is identical intermittent damage patterns between the perforation holes, which signifies that they were modified by the same machine/processor and that they came from a single unknown origin. Additionally, we have identified multiple different brands with matching production codes on the motion picture edge print as well. So we concluded that these different brands were in fact products from the same faceless source. In the midst of color film supply chain shortages and inflation in the aftermath of a pandemic, it seems that opportunists have been purchasing and repackaging this souped leftover motion picture film, and then passing it off as their own new film that they claim to have created as equal to existing products — even applying for malicious trademark registrations with the CNIPA (for both CineStill and 800T) — but most importantly they failed to deliver on quality.




When this film eventually began to find its way into the US and Europe, search engines were yielding dozens of results for listings that were using our trademarks and brand recognition to market and sell them. Their claims and branding were based solely on our research and reputation (benefiting from the amazing work created by photographers on CineStill film over the last 10+ years). These unaccountable suppliers do not openly stand behind their products and support them as CineStill does. It is apparent that they have not done their own testing to assure quality, shelf life, or even technical performance before releasing these products. Instead they rely upon the hubris of assuming that this unknown source(s) is doing exactly what CineStill has done, then erroneously copying CineStill’s specifications and marks as their own — using our results as their proof of concept. These compromised films are produced in a fundamentally different way, and depend heavily on labs and scanners to correct out the base fog and blue stains in post – which yellows or darkens the final image, revealing further imperfections and color shifts.



Samples edited for base fog in post
KODAK has also recently studied some of these “new” films and gave us permission to share what they reported. Even though “They are claiming this to be a ISO 400-speed film,” and “the film’s raw [unprocessed] emulsion color is not significantly changed…the sensitometry of [the motion picture film] is ruined, however, and the pictures being taken [on this film] can not be considered good. A magician in a processing / scanning / printing lab may be able to rescue a decent image, but final prints will have low contrast, low color, and may have very smokey blacks.” EASTMAN KODAK’s “Overall impression is that the [rem-jet removal process] is moving some of the soluble dyes around in the film and…restraining exposure or development. The D-min [base fog] has grown quite a lot…as the molecular places where dye was located are voids that the developer can work into and over develop those low to no exposure grains.”


They also noted that, ”Adjustments to the development time could be made to reduce the D-min effect, but those would also lower the upper-scale density growth [D-max]. A terrible way to trick customers in believing that they will receive good images… flat, and ugly is all that this film will achieve.” KODAK again affirmed that the ”CineStill [Premoval process] is far superior as it has little to no effect on sensitometric curve of the film...” Although this example is just one of the films which KODAK has studied, they concluded that “Others, who may be purchasing motion picture negative from production left-overs, etc., and who try to remove rem-jet…will encounter similar sensitometric deviations” - exhibiting varying degrees of raised D-min (fogged) and restrained D-max (desensitized) with various different films.
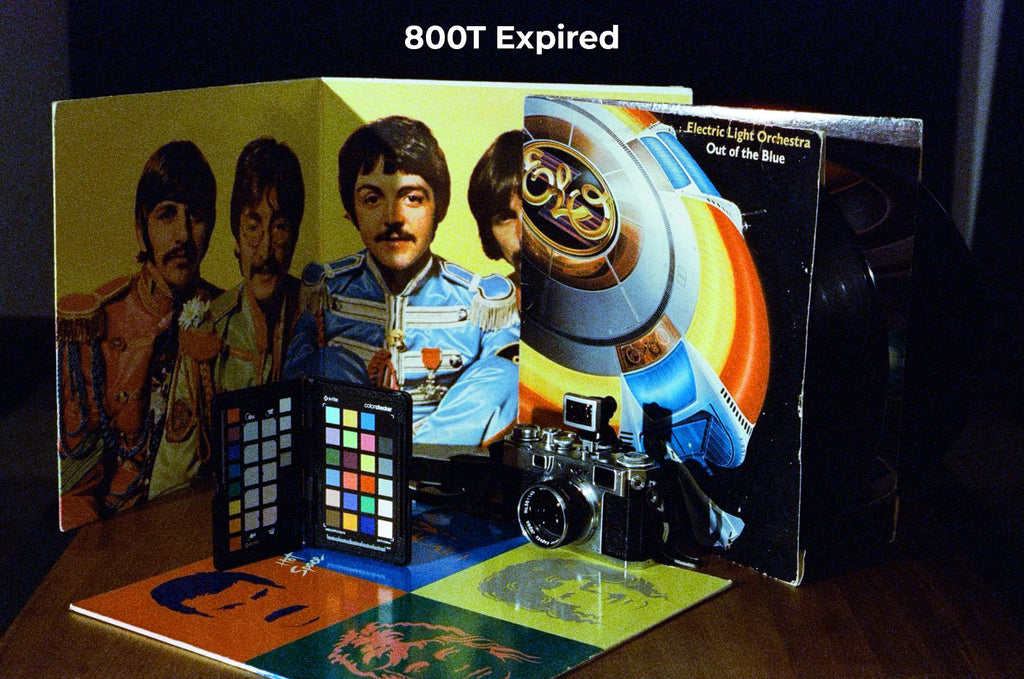
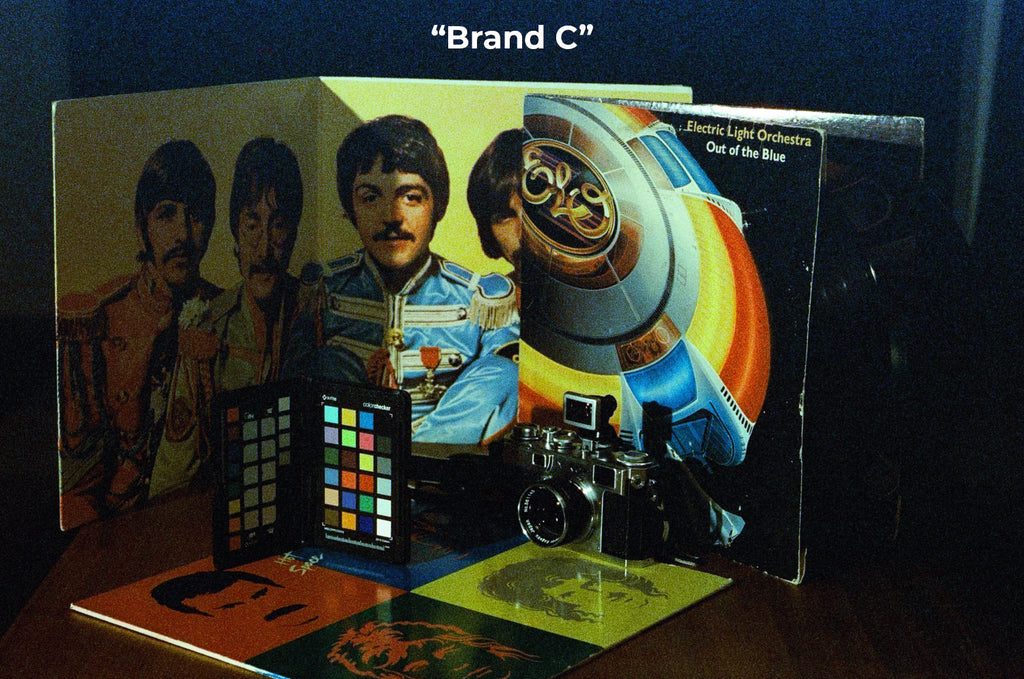


Using the Noritsu minilab scans that were corrected for base fog to match shadow density and color, we compared expired 800T with “Brand C”, both exposed to place the color swatches in Zone 2 and Zone 1 at EI 800. These were once again processed in the same tank at the same time, eliminating any variance in processing. While 800T preserved significantly better detail in all colors all the way down to Zone 1, “Brand C” clearly recorded less shadow detail (especially in the cool tones) than would be expected from an 800 speed film and should be more accurately rated around 400 to preserve shadow detail once corrected. For a brief explanation of The Zone System check out https://www.lifeinedit.com/tutorial-5-the-zone-system/
True 800T
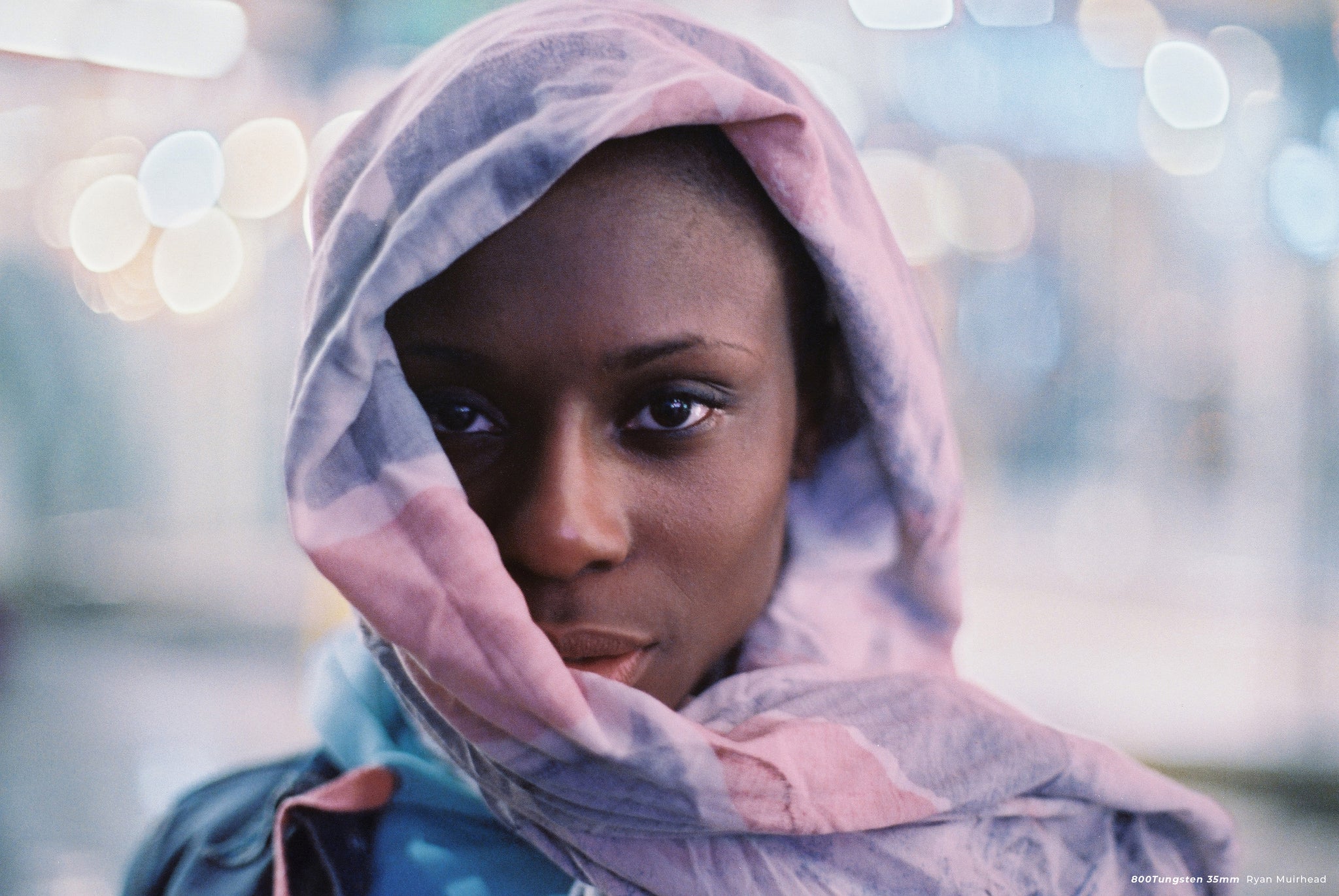
If at any point we had found someone making another truly 800-speed tungsten-balanced film, we would have wanted to support them and work together, or even offered partnership to make even more CineStill 800T available worldwide (if it held up to the quality standards film photographers have come to expect from CineStill) — there just hasn’t been one. It should be made abundantly clear; we have never claimed to own the number “800”, the word “tungsten” or the letter “T.” Nor do we claim that they cannot be used to describe other color films which are tungsten-balanced or 800-speed. And we would never imagine engaging in a dispute on those grounds. The reality is that these rebranded films would be more accurately described as something like, 500Souped or 250Expired motion picture film. As you can see, if they could be fairly described as 800-speed in tungsten light, then 800T really should be 1600T… A bold claim that we could not stand behind!
The real issue arises when some of these ambiguous brands are marketing what they claim to be the exact same as CineStill film or motion picture film and delivering something else entirely — then the burden falls solely on us to address the distinctions. We have always preferred to privately support and help any other business in this small industry, but it seems that there are contentious pretenders and imposters — riding the wakes of renaissance and making waves socially rather than contributing to and uplifting film photography. Some became defensive when we tried to reach out to them, and a few tried to bait us into a legal dispute and even retaliated spitefully with threats and baseless accusations. Even though we realize that it falls upon us to defend our products — rather than engaging in public rows and controversy over what constituted consumer confusion, we’ve sought to keep the film community a respectful and accountable space with healthy competition that is fair to the end user. True 800T, and true CineStill, is more transparent, accessible, and innovative; built on collaboration, serving the community with teamwork, excellence, consistency, and integrity.
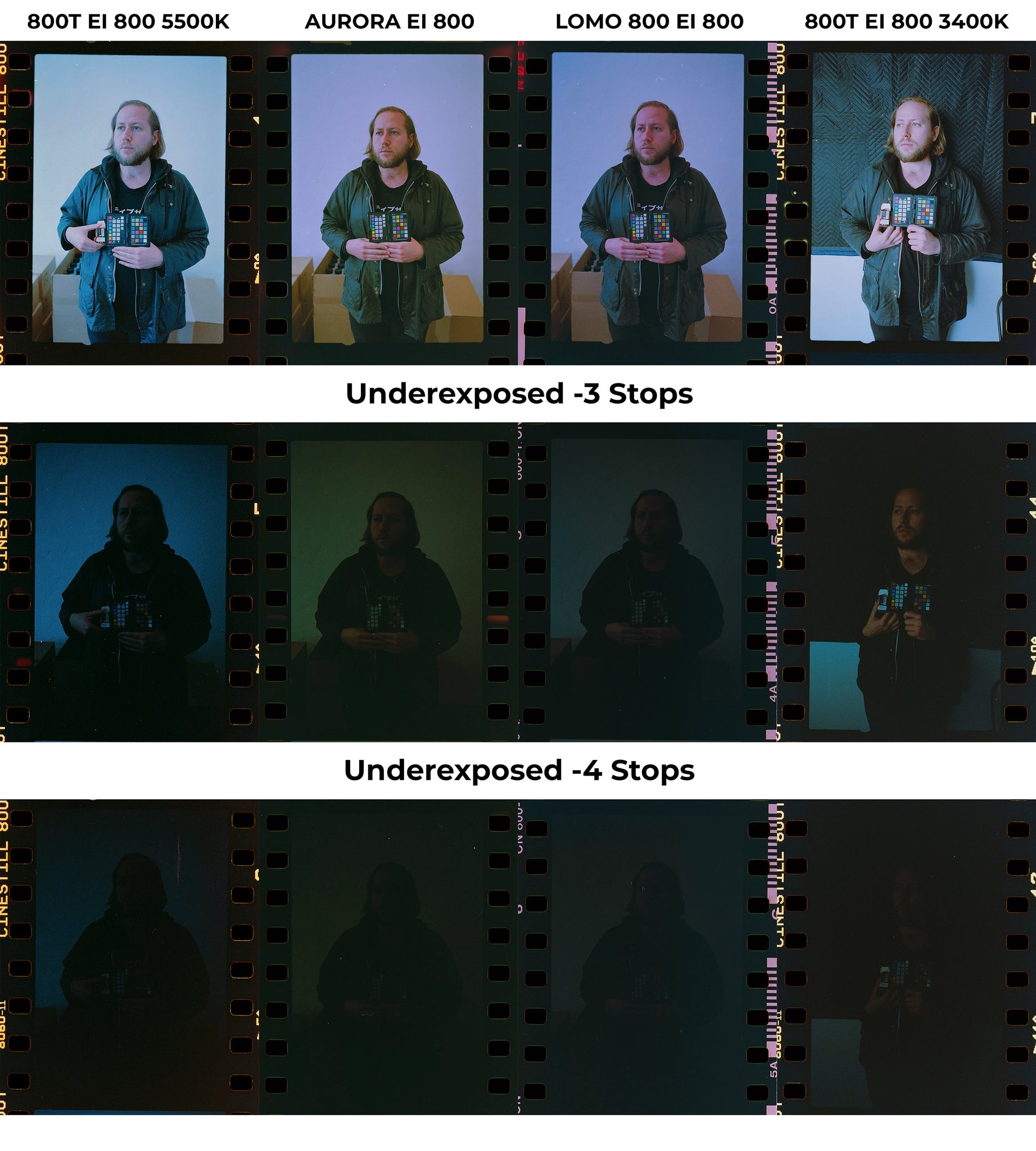
Hopefully this candid PSA can serve to clear up why fresh 800T remains the original and only true 800-speed tungsten-balanced film made for still photography, and may also help to manage the expectations/standards for anyone trying to imitate it. While we don’t have control over the way other businesses make or market their products, we can take solace in our own transparency and hope that our research sheds some light — while supplying a product that delivers on its claims. We go out of our way to avoid bias and remain objective when doing testing and quality assurance, but we understand and encourage anyone wanting to do your own controlled comparisons and see for yourselves… A few already have.If we want to build upon the analog renaissance and improve the experience of shooting film then we can support those who do! We support and have worked with nearly every film manufacturer in the world. We are standing on the shoulders of giants more than 100-years-old, and we couldn’t make film without them or without you. We don’t take anything for granted and we are always collaborating, investing and improving, while maintaining the confidence of our customers and partners by being as open and transparent as we are allowed to be and respecting their autonomy. You can also be a film maker, by making the film manufacturers — whom make the novel analog products we love — make more quality film for film photographers. Shoot and process fresh film, made by brands beyond repute, it doesn’t need to just be CineStill. Support KODAK, Ilford, Harman, ADOX, Ferrania, Polaroid, Fujifilm, FOMA, Ars-Imago, JCH, Kosmo, Film Washi, Kentmere, etc., and most importantly support your local film supplier!

We will continue to work every day to channel our efforts into helping demystify and improve the modern analog photography workflow, and make the highest quality film, chemistry and other tools accessible to help film photographers create their best work. As always, we are here for the community and are excited to share what’s next.
Share this post
- 1 comment
- Tags: 135, 1600, 3200, 35mm, 400D, 500Tungsten, 5219, 800T, 800Tungsten, beta test, C-41, cinema film, cinestill35mm, color, color photography, colour, comparison, eastman, ECN-2, High ISO, imitation, Test, tests
Great post. So much information, real information. Next time I will try Cinestill 400D. Thanks